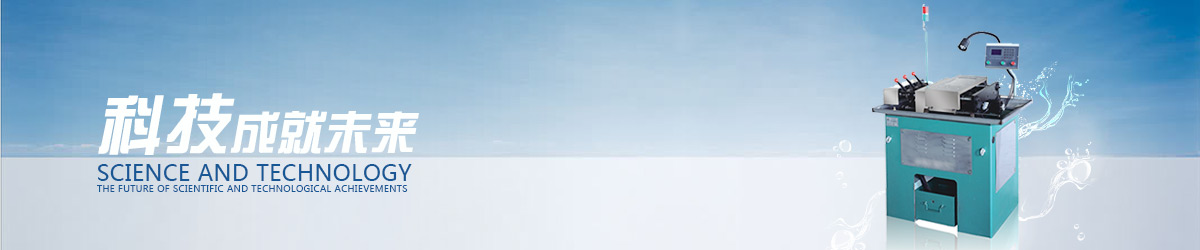
Introduction of sintered neodymium iron boron plating process
As we all know, the most commonly used in the production of neodymium iron boron electroplating process can be divided into two kinds of rolling and hanging, this paper focuses on the process of roll plating.
Base specific process is as follows: baked in oil closed rolling light washed a barrel (steel ball and with a ultrasonic except oil washing a washing with water and acid etching a water washing to film a washing a washing activation ultrasonic cleaning barrel plating to washed out of the slot a washing with water and drying.
There are several processes in the process is the conventional plating process is not, is the product of the characteristics of the design of the process, to pay special attention to.
(1) bake in addition to oil
Neodymium iron and boron products are similar to powder metallurgy products of porous sintered materials, in the process of processing will inevitably have dirty dirt into the hole and not easy to clear. Simple method is the use of strong oxidation of the air temperature, the inner hole of the oil evaporation or ashing, to eliminate future caused by node force bad risks.
(2) closure
Closed on porous materials commonly used surface treatment method, the common method can use powder metallurgy closure method, i.e. leaching method of zinc stearate, zinc stearate in metal containers are heated and melted (130 to 140 DEG C) and then baked in oil product is immersed in the molten zinc stearate to, leaching for 25 minutes or so. Out in the oven at 600 C dry 30min, or at room temperature for more than 2h, so that the curing.
(3) rolling light
After the closure of parts also rolling light treatment, the surface oxide, burr, sealant after rolling light processing are removed and showing a new crystal metal surface. The use of abrasive regards the surface condition and different, usually for wood plant hard material, also available artificial abrasives (artificial pumice, etc.). The ratio of the workpiece to the abrasive is 1: (2 ~ 1). In order to improve the rolling effect, we can add a little 0P emulsifier, the amount of water to drown the workpiece is appropriate, the barrel is good, the speed is 30 ~ 40r/min, the time is 30 ~ 60min.
(4) to film
The removal of the film is due to the surface layer of a layer of black film remaining on the surface of the product after the acid etching. If not removed, it will affect the adhesion of the coating. And the black film should not be used to general acid removal, can add 15g / L of organic acids in 150ml concentrated hydrochloric acid, at room temperature treatment was about 2 minutes can be.